HOT PRODUCTS

ABOUT US
Guangdong KINGRUN Technology Incorporation
We are founded in Dongguan of China in the year of 2011. Taking the advantage of being located in the core manufacturing area of China South. KINGRUN has developed to be an excellent die caster providing many types of precision casting components which are widely used worldwide.
FOUNDED IN 2011
+
20 YEARS EXPERIENCE
+
MORE THAN 100+ PRODUCTS
$
MORE THAN 10 MILLION

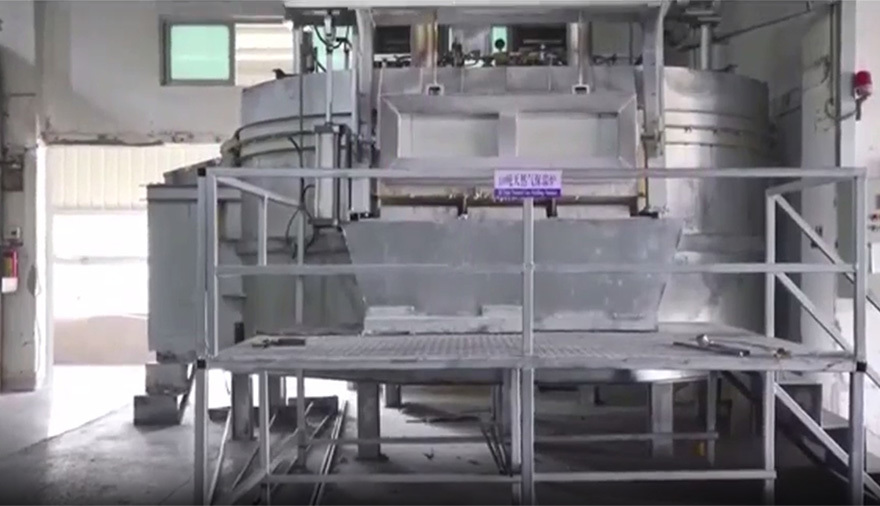
OUR ADVANTAGE

Quality Assurance
Quality Assurance
ISO9001:2015 Certified.
IATF16949:2015 Certified.
GB/T24001:2016/ISO:14001:2015
Spectrometer,CMM etc. equipment for Quality Assessment.

New Building New Machines
New Facilities
10 sets of Casting machines from 280 to 1,650 tons.
130 sets of CNC machines including LGMazak and Brother
New impregnation line.
New Chrome plating line.
New powder painting line.
New assembly line.

28 Years Casting Experience
28 Years Casting Experience
Early started as casting mold maker in middle 1990’s
Casting manufacturing was established since 2011.

Quality
Our Mission
Provide stable quality and reliable service to all our customers.
The faith is we never disappoint the customers when we can do it.
FOCUS ON NEWS
A Global Supplier of World-Class Fabricated Products-Aluminum die casting
2024-09-24
Kingrun provides superior quality custom die casting parts and components for a wide range of industries including automotive, telecommunications, machinery, electrical, energy, aerospace, submarine and others. Our die casting machines range from 400 up to 1,650 metric tons, we can produce die casting parts from a few grams to more than 40 pounds with superior quality ready for assembly. For die casting parts with requirements of esthetical, functional, or protective coatings, we also offer a broad range of surface finishing including powder coating, e-coating, shot blasting, chrome plating finish. Kingrun in-house tooling facilities and component foundries have an annual production capacity of more than seven million raw or machined cast parts involving any combination of the following processes Tooling design and build Melting Casting and trimming Surface treatment by shot blasting and tumbling Heat treatment CNC machining Various testing and quality assurance processes Simple assembly of ready-to-build unit Before a designer or engineer can utilize aluminum die casting to its full potential, it’s important that they first understand the design limitations and common geometric features that can be accomplished with this manufacturing technique. Here are some factors that you should keep in mind when designing a part for aluminum die casting. Draft – In aluminum die casting, the draft is considered as the amount of slope given to the cores or other parts of the die cavity, which makes it easier to eject the casting from the die. If your die cast is parallel to the opening direction of the die, the draft is a necessary addition to your casting design. If you optimize and implement a proper draft, it will be easier to remove the aluminum die casting from the die, increasing precision and resulting in higher quality surfaces. Fillet – The fillet is a curved juncture between two surfaces that can be added to your aluminum die casting to eliminate sharp edges and corners. Parting line – The parting line is the point where two different sides of your aluminum die casting mold comes together. The parting line location represents the side of the die that is used as the cover and which is used as the ejector. Bosses – When adding bosses to aluminum die casting, these will act as mounting points for parts that will need to be mounted later on. In order to optimize the integrity and strength of bosses, they should have the same wall thickness throughout the casting. Ribs – Adding ribs to your aluminum die casting will grant more support to designs that need maximum strength while still maintaining the same wall thickness. Holes – If you need to add holes or windows into your aluminum die casting mold, you’ll need to consider the fact that these features will grip to the die steel during the solidification process. To overcome this, designers should integrate generous drafts into hole and window features. Welcome to contact Kingrun through info@kingruncastings.com.
What is precision die casting?
2024-09-24
High precision die casting is a crucial process in the manufacturing industry, playing a significant role in the production of complex and intricate metal components. This advanced manufacturing technique involves injecting molten metal into a steel mold, known as a die, under high pressure. The result is the creation of high-quality, dimensionally accurate parts with excellent surface finishes. This process is widely used in various industries, including automotive, aerospace,Telecommunications, and medical equipment manufacturing. One of the primary advantages of high precision die casting is its ability to produce parts with tight tolerances and intricate designs. This level of precision is essential for industries that require components with complex geometries and fine details. The process allows for the production of parts with thin walls, sharp corners, and intricate features, making it an ideal choice for applications where precision is paramount. What is precision die casting The high precision achieved through die casting is attributed to the use of advanced technology and state-of-the-art equipment. Computer-aided design (CAD) and computer-aided manufacturing (CAM) software are utilized to create highly detailed molds that accurately replicate the desired part geometry. Additionally, the use of advanced die casting machines with precise control systems ensures that the molten metal is injected into the mold with exceptional accuracy, resulting in parts that meet the most stringent quality standards. Furthermore, high precision die casting offers excellent repeatability, meaning that parts can be consistently produced with minimal variation from one batch to another. This level of consistency is crucial for industries where uniformity and reliability are essential. Whether producing small or large quantities of parts, high precision die casting ensures that each component meets the specified requirements, leading to enhanced product quality and performance. In addition to precision and repeatability, high precision die casting also offers cost-effective manufacturing solutions. The ability to produce complex parts in a single operation reduces the need for secondary machining processes, resulting in lower production costs and faster time-to-market. This makes high precision die casting an attractive option for companies looking to streamline their manufacturing processes and optimize production efficiency. The versatility of high precision die casting extends to the wide range of materials that can be used, including aluminum, zinc, magnesium, and copper-based alloys. Each material offers unique properties and benefits, allowing manufacturers to select the most suitable alloy for their specific application requirements. Whether it’s lightweight components for the automotive industry or corrosion-resistant parts for the aerospace sector, high precision die casting can accommodate a diverse range of material needs. As industries continue to demand higher quality and more complex components, the role of high precision die casting in modern manufacturing is becoming increasingly vital. Its ability to produce intricate, high-quality parts with exceptional precision and efficiency makes it a cornerstone of advanced manufacturing processes. With ongoing advancements in technology and materials, high precision die casting is poised to remain a driving force in the production of high-performance components for a wide range of industries.
KNOWLEDGE